Vibratory Furnace Charger consists of a vibrating feeder mounted on a moving trolley with a storage hopper mounted above the feeder. Our company make vibratory furnace chargers basically comprise of the following parts. Vibrating Feeder is suitable for delivering required capacity, storing hopper of required capacity, moving carriage with driving arrangement. Control panel for operating the system. Cable reeling Drum / Cable Drag Chain.
The metallic components like scrap, bales, pig iron and foundry retains are stored in the hopper. The hopper shape is specially designed to enable bulky and irregular scrap pieces to be extracted without problem.
Vibrating furnace charger is effective solutions to problems such as high labor cost, hazards operators faced in foundries, melting shops etc. Such a kind of automation allows foundry men to work at a safe distance thus preventing injuries arising out of molten metal splash. It also facilitates in rapid and quick charging of the furnace thereby allowing maximum utilization of the furnace, in addition to this, the damage to furnace lining is avoided which normally occurs in manual charging of the furnaces.
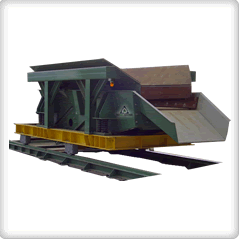
WORKING PRINCIPLE:
The required amount of scrap metal is loaded into the storage hoper at the loading point. The trolley the carries the vibrating feeder along with the storage hopper to the furnace charging point. Here, the vibrating feeder is energized and the material is effectively discharged into the furnace as per the required capacity. As the metal is melted down, fresh batch of metal can be fed into the furnace thereby keeping the furnace full. The capacity of the vibrating feeder can be varied by varying the amplitude of variations. The amplitude of vibrations can be varied by adjusting the position of centrifugal weights or by using a variable frequency drive (optional). A control panel specially designed to suit individual client requirement depending on the sequence of operations required is provided.
FEATURES AND ADVANTAGES:
- Very fast as compared to manual charging of furnace thereby enabling optimum use of the melting system
- Minimum heat loss of the furnace since the charging process can be maintained continuously at the required rate
- Extremely controlled charging of material into the furnace
- Prevents damage to the furnace lining since the material is properly guided into the furnace so as to avoid the material from hitting the furnace walls
- No direct exposure of manpower to the furnace thereby preventing dangerous accidents due to metal splash (since the operator can carry out the operations at a very safe distance.)