Introductions:
The rotary dryer is the material heating and drying device. The materials in the rotary cylinder coaxial sets of columns by the spiral blade and interrupted spiral lifting plate to dry in the process of reentry and lifting between the inside and outside the cylinder. Sleeve sets of column structure so that the length of the dryer can dynamic substantially reduced due to the cooling surface, so that the heat consumption decreased, and the doubling of the heat exchange surface greatly improve the thermal efficiency.
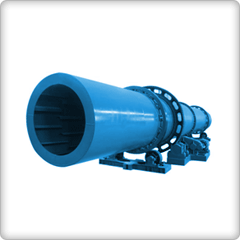
Working Principle:
The cylinder of dryer is a rotary cylinder which is oblique slightly. The materials are fed from the relatively higher terminal, heat carrier comes in from the lower terminal, and sometimes the heat carrier and materials get into the cylinder together.
The wet materials are transported into the material hopper by the belt conveyor and bucket elevator, and gets into the feeding terminal through feeding pipe with the aid of feeder of material hopper. The pitch of the feeding pipe should be more than the natural pitch of materials in order to help the materials flow into the dryer successfully. Along with the revolving of cylinder, the materials move to the lower terminal due to the gravity.
When the wet materials move forward, it receives the heat from the heat carrier directly or indirectly. As a result, the wet materials are dried, and discharged out by belt conveyor or screw conveyor on the outlet. There is shoveling plate inside the cylinder in order to shovel materials up and cast it out, to increase the connection surface, to promote drying efficiency, and accelerate the forward movement of materials. Generally, the heat carrier can be hot air and chimney flue. After the heat carrier is dried, the materials mingled with air should be collected with cyclone dust collector. If there is need to reduce the content of dust mixed with tail gas, the heat carrier should be subject to bag dust collector or wet dust collector before it is discharged.
Features:
- Uniformity of drying product is good
- Simple and excellent structure, material running smoothly through the cylinder, operating convenience
- Less mechanical failure, low maintain charge, low power consumption
- High degree of mechanization, large production capacity, continuous option
- Drying production line using a special scattered installations to ensure the dryer’s drying effect
- Cassava dregs dryer Use innovative and unique sealing device, and sophisticated keep-warm system. Thus reduce the coal consumption of the system effectively
- The whole system holds a good performance of sealing. It also has a complete dust removal equipment. There is no dust spilling. It still has a good operating environment
- The whole drying system uses electric centralized control, auto-control of temperature for hot air, high automation and convenient operation
- You can join in crushing ,mixing ,granulating, packing and other follow-up steps after drying to produce the finished product of bean dregs particle feed
Applications:
Rotary Dryer is mainly used for metallurgy, building materials, ores and other mineral materials, heating and calcining. Such as ceramic sand, bauxite, limestone, cement, fly ash magnesium aluminum hydroxide, aluminum products, alumina refractory materials such as mineral particles and the heating and calcined powder.